In recent years, the global supply chain has been overwhelmed by never-ending and ever-increasing parcel flows, leaving shippers and their associates desperate for solutions to manage volume efficiently and effectively.
That’s where Jay Tobia comes in. Jay is the Head of Product here at Ambi Robotics, where we create tools for people to solve real-world problems, like the grand challenge of parcel sortation. Here, Jay talks about how Ambi Robotics enables robots to work hard so people can work smart and boosts operational performance that shippers can see in throughput speeds and immediate return on investment.
1: How challenging is it these days for shippers to adopt new technologies?
“The AmbiSort A-Series makes it as straightforward as possible to adopt new technology for parcel sortation. On the item handling side of things, the machine is able to handle the same parcel range that our customers were manually sorting before. As far as customer and operator adoption, we do a lot of things to make the adoption as seamless as possible.”
“First, we provide some amazing hands-on training to get operators excited about using the systems. Next, the system has a lot of features that make it easy to use. We have videos and images embedded in the human-machine interface touchscreen, showing operators how to troubleshoot any issues they encounter. There are indicators around the machine that show when bags are full, or when the machine needs a new bin of parcels. The system really makes the manual sortation job less monotonous, less strenuous, and overall more enjoyable. Even when we’ve seen hesitancy from operators during install, we’ll come back a month later and have those same operators be some of the best and most enthusiastic robot operators in the building.”
2: How do AmbiSort sorting systems ease that transition for shippers and unlock operational optimizations?
“It’s an automated system that has enough capabilities to augment a truly manual and monotonous process. Traditionally, automation in robotics was not able to deal with the types of variation in parcel types that manual workers handle. So with the Sim2Real technology that we leverage at Ambi, we’re able to deal with that wider range of parcels in a more robust way and meet the bar of being able to replace that manual process.”
“And then, our technology can adapt on-the-fly to process the same types of parcels that the manual processing does and accept them in a similar way to the manual process. So, we’re able to integrate very easily to customers within their warehouse environments. It has the ability to fit almost anywhere within a warehouse’s relatively tight footprint and requires minimal intervention to maintain a high parcel sorting throughput.”
3: You mentioned Sim2Real technology, a virtual training in the AmbiOS operating system that enables AmbiSort robots to sort anything accurately on day one. How does that technology truly make a difference in the warehouse?
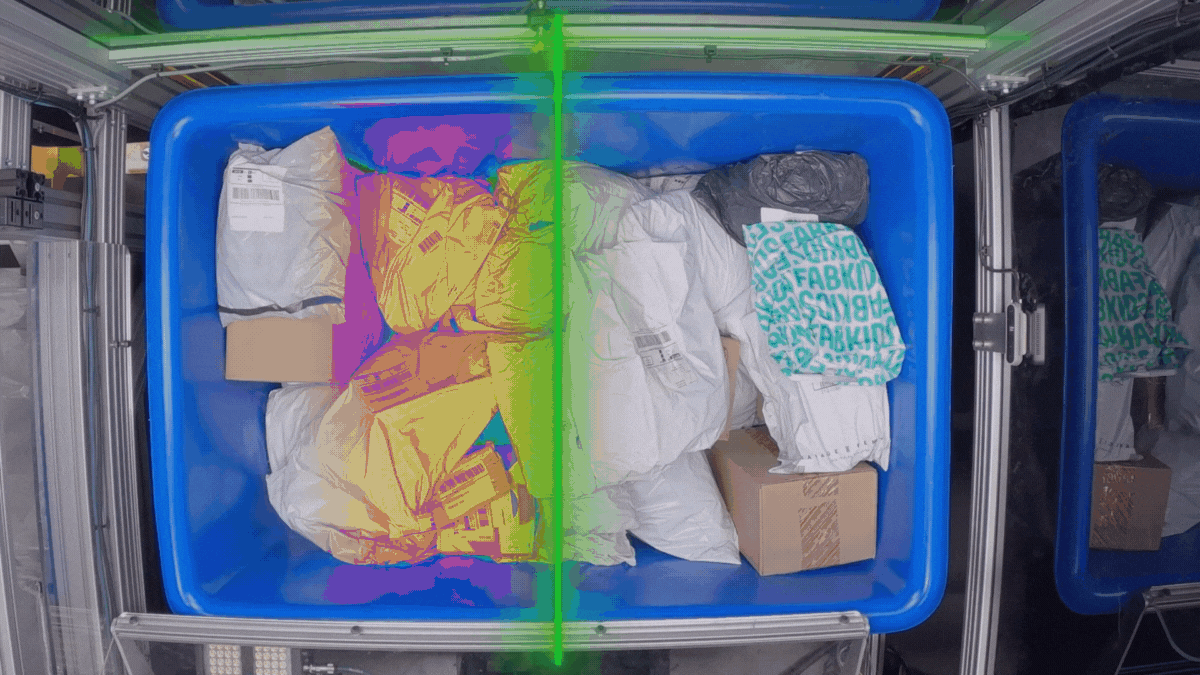
“Traditionally, package-sorting is done by people actively maneuvering packages to relocate barcode surfaces to face-up for better scanning performance. Sim2Real virtually trains robots to pick packages in many different forms so it can start sorting parcels 10,000 times faster than traditionally trained robotic systems.”
“It enables our robots to handle a wide variety of packages in their unstructured, unorganized way … you can just feed the bins with mixed parcels. The parcels don’t need to be the same every day. We don’t need to see them beforehand. You just feed your typical parcel flow to the system and it begins processing them. That’s one of the strong points of the technology. And sometimes we almost forget about it, because the system does it so well. But it’s really what makes this type of technology possible, and it gives us the ability to replace the manual sortation process.”
4: How does Ambi Robotics make robotics more accessible to customers? Can you share more about your unique Robotics-as-a-Service (RaaS) approach and how RaaS enables shippers and logistics companies to unlock immediate Return on Investment (ROI)?
“The way it boils down is, our monthly robot cost is less than the manual cost incurred in the former process. The monthly robot cost plus the labor it takes to operate those systems is less than the manual processes. And that’s true because our systems maintain high throughput with low operator intervention, as well as sort more accurately than the manual process … you’re not having to pay a high capital expenditure, and then make back money over time. Instead, this cost is already broken up into an operational cost for the customer.”
5: What is the most common question you receive from shippers?
“One of the biggest questions is about return on investment. We talk about how a single operator can maintain high throughput on many systems at the same time, as opposed to a manual sortation process where there’s one operator doing an inconsistent amount of throughput with a relatively high inaccuracy rate.”
6: How do companies like Ambi Robotics ensure ongoing customer satisfaction?
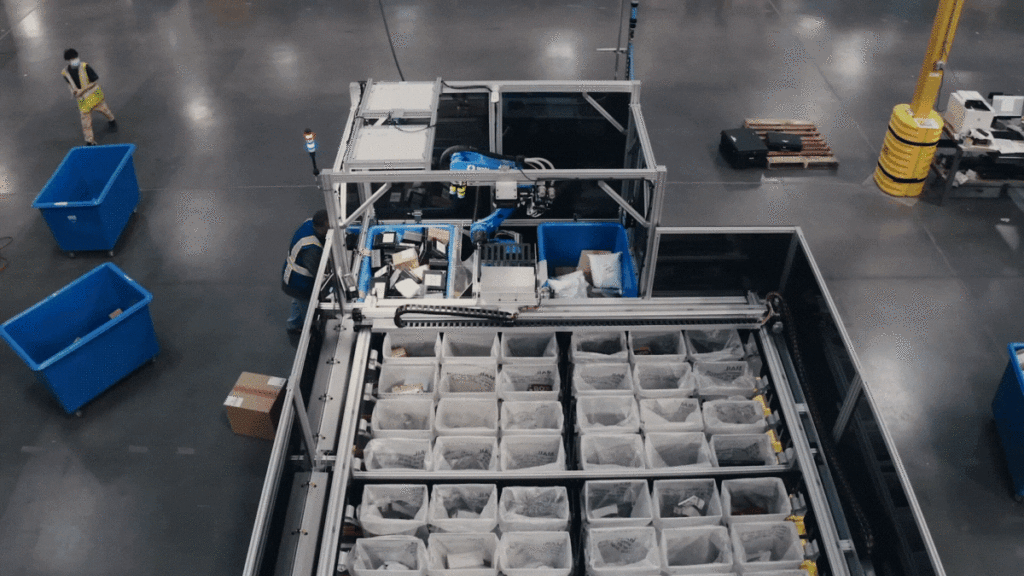
“The system just needs to work in the field. And so we do that by providing support – as well as continuous software updates – in order to improve our handling of parcels over time, as well as incorporate more specific customer feedback. Even if it’s the color of lighting, or how fast it’s blinking, or their integration with how they’re planning their sort plans, that’s something that we’re able to tailor the finer points of the solution to the customer’s exact needs. It enables our product to fit more seamlessly into their production workflows, and the more seamlessly it fits in and the smoother it is for them to use, they adopt more as it is more beneficial for their business.”
“We don’t want to hold back a customer from utilizing the system. Some of our biggest goals are handling the parcels at high throughput consistently over the day, and that’s what we consistently aim to improve through software updates and even training resources.”
7: What is your advice to shippers and warehouses considering optimizing efficiency through technology upgrades?
“The robotic solutions we’re putting together have reached a point where they are easy to maintain, and they’re able to deal with the wide variety of packages that you see in typical parcel shipping. Customers shouldn’t hold themselves back from pursuing this type of solution because they feel that the process is too difficult to automate. Our systems are sorting millions of packages per week across the country. The innovation that we put together makes it so that that’s not a concern anymore.”
“With us, you can focus more on operating the solution and doing preventative maintenance and elevating the working conditions, rather than worrying about some fundamental parcel-handling issue.”
Ready to Handle More?
Are you ready to start solving your problems with real world solutions? Join us on our mission to empower humans to worker smarter with the help of AI-powered robots. Check out our open positions and let us know if you see an interesting fit.
The post We Asked Our Head of Product 7 Questions on How AI-Powered Robotics Enable Shippers to Solve Real-World Problems appeared first on Ambi Robotics Inc..